Introduction
Structural work is a crucial aspect of any construction project. It is critical to understand the importance of proper fastening and torquing bolts, especially when dealing with steel and aluminum. If you don’t follow these rules, then your structure may fall apart when subjected to stress or pressure.
Torquing 101
Proper fastening of steel and aluminum is done by torquing the related bolts. Torquing is the the process of tightening a bolt. The most common way to measure this is with a torque wrench that has an adjustable scale gauge, which indicates how much torque has been applied. Torque is the turning force applied to a bolt or nut that can be measured in foot-pounds (ft-lb) or Newton meters (Nm). The unit for measuring torque is the pound-foot (lbf ft), which means pounds multiplied by feet.
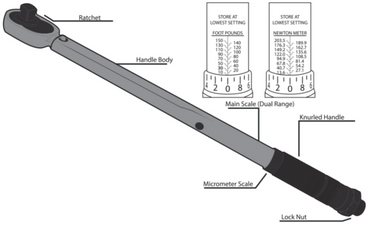
If your bolt is not properly torqued it will loosen when the appropriate force has been applied on it. This can have serious consequences as loose bolts may fail to hold the structure together causing damage.
Structural Work
A structural bolt needs to be able to withstand a certain amount of force before it fails and it’s crucial that bolts are tightened with enough torque so that they don’t fail prematurely. The first reason for this is obvious: if a bolt were to fail, the structure could collapse and have dramatic consequences. The second reason is less obvious but still important: if you don’t tighten your bolts correctly, then they won’t fit as tightly into their respective nuts or holes in which they sit—this could cause problems both now and in future decades when changing weather conditions affect how much pressure must be put on these pieces of hardware in order for them all work together effectively.
If you want to ensure that your bolts are properly tightened, then it’s wise to use a torque wrench. The right tool can help you avoid over-tightening the screws which can cause damage to both the nuts and bolts. Over-tightening can also cause damage to the structure itself, so this is something you want to avoid.
How to Reduce the Risk of Errors
In the past decades, we have seen many industries try to reduce the risk of errors due to bolt torquing. Indeed, torquing bolts, although a pretty simple operation, can be a major source of non-conformities when it’s done on the job site. Therefore, many businesses are now choosing to preassemble their product at their facility, therefore torquing the bolts in a controlled environment. REMAC, for example, is offering preassembled aluminum towers for many industries, including telecommunications. The preassembly has allowed REMAC to reduce the risk of errors by 94%.
Conclusion
There are many benefits to properly torquing your bolts. The most important one is that it ensures that your structure does not come loose and fall down. When dealing with structural work, we need to consider many factors before proper torquing such as material strength and thickness. Moreover, we have to ask ourselves “how much force will we apply on the bolt?